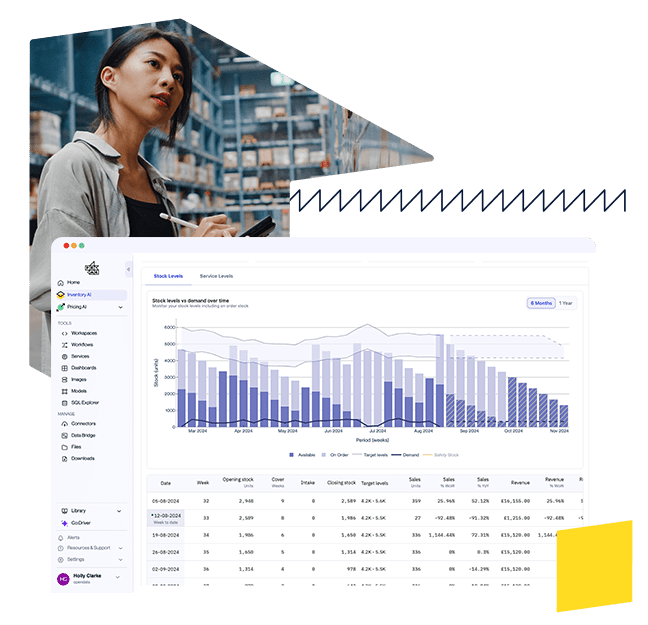
Inventory AI | Dynamic Inventory
Balance inventory and service levels
Inventory levels can make or break a business. Get a smart view of your stock with inventory planning, optimization and management software
Balancing service and inventory levels is hard
How can you accurately forecast inventory levels on products or materials with unpredictable demand? The answer is Peak’s dynamic inventory optimization management software. Its AI models help you hit the perfect levels of service and inventory, meaning you don’t miss out on a sale.
Right product, right place, right time
Peak’s dynamic inventory planning software puts AI to work on your inventory, order, product, location and historical sales data. It optimizes your demand forecast accuracy to plan the ideal level of inventory across your network.
Optimize safety stock levels
Maximize margins, while avoiding stockouts, wastage and unnecessary costs across your entire distribution center network with our dynamic inventory optimization solution.
-
Maximize availability, margin and hit sales targets
-
Meet SLAs and OTIF
-
Optimize safety stock levels
-
Reduce stockouts, wastage and freight costs
-
Free up working capital
See Peak's inventory management software in action
See Inventory AI’s Dynamic Inventory module in action. Hit the button below to take a quick tour, or watch the 30-second overview video.
Under the hood
Dynamic Inventory is a piece of inventory planning, optimization and management software that’s built on Peak, an AI platform built to drive growth, profit and efficiency. Demand forecasting and safety stock models are used to recommend reorder points and optimal inventory levels at each distribution center location, helping you meet service levels efficiently.
- Key users
- Features & benefits
- Actions and results
FAQs
What is Dynamic Inventory?
Dynamic Inventory is an application that uses AI to accurately forecast demand and set target inventory levels at each location; balancing sales, service and availability with the costs of holding too much inventory.
Dynamic Inventory applies AI models to inventory, sales and product data from across your business. It allows you to more accurately forecast demand and get the right product, in the right place, at the right time to meet your targets.
In wider usage, the term dynamic inventory refers to a constantly evolving and real-time system of managing and updating inventory levels, providing businesses with a more flexible and responsive approach to stock control. In the context of supply chain management, dynamic inventory allows organizations to adapt to fluctuations in demand, market trends and unforeseen disruptions.
By employing dynamic inventory systems, businesses can optimize their stock levels, reduce carrying costs and enhance overall operational efficiency. This approach often involves the use of advanced technologies and software solutions that automate inventory tracking, reorder processes and demand forecasting.
Implementing dynamic inventory management can have significant benefits, including improved accuracy, better customer service and increased cost-effectiveness. It empowers businesses to stay agile in a rapidly changing market, ensuring they can meet customer demands promptly and minimize the risk of overstock or stockouts.
In summary, dynamic inventory is a strategic approach to inventory management that leverages technology and real-time data to create a more adaptive and responsive supply chain, ultimately contributing to improved business performance and customer satisfaction.
What is inventory optimization?
Inventory optimization is a crucial strategy for businesses aiming to enhance efficiency and profitability in their supply chain management. It involves utilizing advanced tools and methodologies to strike the right balance between maintaining adequate stock levels and minimizing excess inventory costs.
In essence, inventory optimization ensures that businesses have the right amount of stock at the right time, avoiding both stockouts and overstock situations. By leveraging data analytics, demand forecasting and other technologies, companies can streamline their inventory processes and make informed decisions about when and how much to order.
Effective inventory optimization leads to a range of benefits, including reduced carrying costs, improved order fulfillment and increased customer satisfaction. It helps businesses align their inventory levels with actual demand, preventing shortages that can result in lost sales or excess stock that ties up capital.
In today’s competitive market, where customer expectations are high, implementing inventory optimization practices is essential for staying agile and responsive. By embracing these strategies, businesses can achieve a leaner and more cost-effective supply chain, ultimately driving long-term success.
In summary, inventory optimization is a data-driven approach to managing stock levels efficiently, contributing to improved operational performance and customer service. Embracing these practices positions businesses for success in a dynamic and competitive marketplace.
What are the benefits of inventory optimization?
Inventory optimization offers a myriad of benefits for businesses seeking to streamline their supply chain and enhance overall operational efficiency. Here are some key advantages:
- Cost reduction: By aligning inventory levels with actual demand, businesses can minimize carrying costs associated with excess stock. This leads to lower storage expenses, reduced depreciation and enhanced financial performance.
- Improved cash flow: Inventory optimization helps free up capital tied to excess stock, allowing businesses to invest in other critical areas of operations. This improved cash flow contributes to financial flexibility and strategic growth opportunities.
- Enhanced customer satisfaction: Maintaining optimal inventory levels ensures that products are consistently available to meet customer demand. This reduces the risk of stockouts, prevents delays in order fulfillment and ultimately enhances customer satisfaction and loyalty.
- Accurate demand forecasting: Inventory optimization relies on data analytics and forecasting tools to predict demand patterns more accurately. This enables businesses to make informed decisions about when and how much to reorder, minimizing the likelihood of both shortages and overstock situations.
- Operational efficiency: Streamlining inventory processes through optimization leads to increased operational efficiency. Automation of reordering processes, real-time tracking and data-driven decision making contribute to a more agile and responsive supply chain.
- Reduced lead times: By understanding demand patterns and maintaining optimal stock levels, businesses can reduce lead times in the procurement process. This agility allows for quicker response to market changes and customer needs.
- Strategic planning: Inventory optimization provides valuable insights into product performance and market trends. This data-driven approach empowers businesses to make strategic decisions regarding product lines, promotions and overall inventory management.
- Mitigation of obsolescence: Regularly optimizing inventory helps identify slow-moving or obsolete stock. By addressing these issues promptly, businesses can minimize the financial impact of outdated inventory and prevent losses.
- Competitive advantage: A well-optimized inventory system allows businesses to stay ahead of the competition by adapting to market changes more effectively. This agility is particularly crucial in industries with rapidly evolving trends and customer preferences.
In conclusion, inventory optimization is a multifaceted strategy that goes beyond cost reduction, encompassing improved customer satisfaction, strategic planning and a competitive edge. Businesses that embrace these benefits position themselves for sustained success in today’s dynamic and competitive marketplace.
What is the difference between static inventory and dynamic inventory?
Understanding the difference between static inventory and dynamic inventory is crucial for effective supply chain management. Here’s a breakdown to help clarify these concepts:
- Static inventory: Static inventory refers to a fixed and predetermined stock level that remains constant over a specified period. Businesses using static inventory systems typically rely on traditional methods for order management and restocking. This approach tends to be less adaptive to changes in demand, market trends or unforeseen disruptions.While static inventory may work well for stable and predictable demand scenarios, it can lead to challenges such as overstocking, increased carrying costs and potential stockouts during periods of fluctuating demand.
- Dynamic inventory: Dynamic inventory, on the other hand, involves a real-time and continuously evolving approach to stock management. Businesses employing dynamic inventory systems leverage advanced technologies and data analytics to adjust stock levels based on current demand, market conditions and other relevant factors.Dynamic inventory systems allow for greater adaptability and responsiveness. By constantly updating stock levels and automating reorder processes, businesses can optimize their inventory, minimize carrying costs and ensure they have the right amount of stock to meet customer demand promptly.
Key differences between static inventory and dynamic inventory:
- Adaptability: Static inventory is rigid and less adaptable to changes, while dynamic inventory is flexible and responsive to real-time data
- Automation: Dynamic inventory often involves automated systems for reorder processes, whereas static inventory systems may rely on manual calculations and periodic reviews
- Risk mitigation: Dynamic inventory helps mitigate the risks of overstock or stockouts by adjusting stock levels in response to changing market conditions. Static inventory may be more susceptible to these risks due to its fixed nature
- Efficiency: Dynamic inventory systems contribute to increased operational efficiency by leveraging technology for real-time tracking and decision making. Static inventory systems may require more manual effort and can be less efficient in responding to market dynamics.
The main difference between static inventory and dynamic inventory lies in the adaptability and responsiveness of the inventory management approach. While static inventory provides stability in predictable conditions, dynamic inventory offers a more agile solution for businesses operating in dynamic and fluctuating markets. Understanding these distinctions is crucial for businesses looking to optimize their supply chain and stay competitive.
What is the optimal level of inventory?
Determining the optimal level of inventory is a critical aspect of effective supply chain management, and it involves finding the right balance to meet customer demand without incurring unnecessary costs. While there isn’t a one-size-fits-all answer, several factors influence the optimal inventory level for a business, including demand variability, lead times and customer service goals. Here’s a closer look at some of these factors, and more, in detail:
- Demand variability: The level of demand fluctuations in the market plays a significant role. Businesses experiencing high demand variability may need to maintain a higher safety stock to prevent stockouts during peak periods.
- Lead time: The time it takes for suppliers to deliver new inventory impacts the optimal stock level. Longer lead times may necessitate holding higher levels of inventory to avoid disruptions in supply.
- Customer service goals: Businesses with a strong emphasis on customer satisfaction may choose to maintain higher inventory levels to ensure prompt order fulfillment and reduce the risk of stockouts.
- Carrying costs: The costs associated with holding inventory — such as storage, insurance and depreciation — need to be balanced. The optimal level minimizes carrying costs while meeting customer demand.
- Ordering costs: On the flip side, frequent orders incur additional costs. Finding the optimal inventory level involves minimizing ordering costs without compromising on stock availability.
- Technology and automation: Leveraging advanced technology and automation in inventory management can help optimize stock levels by providing real-time data, accurate demand forecasting and automated reorder processes.
- Seasonal trends: Businesses experiencing seasonal fluctuations must consider these trends in determining the optimal inventory level. It may involve adjusting stock levels based on anticipated changes in demand.
- Market conditions: The competitiveness and volatility of the market influence the optimal inventory level. Businesses in dynamic markets may need to adopt a more flexible approach to inventory management.
In essence, the optimal level of inventory is a delicate balance between meeting customer demand and minimizing associated costs. Businesses should conduct regular assessments, utilize data analytics and embrace technological solutions to fine-tune their inventory management strategies.
By considering these factors and implementing best practices, businesses can strive to maintain an optimal inventory level that aligns with their unique operational requirements and market dynamics. Continuous monitoring and adjustment are key to adapting to changing conditions and ensuring sustained success in the ever-evolving business landscape.