Safety stock vs. reorder point: balancing cost and inventory management
By Jon Taylor on September 7, 2023 - 10 Minute ReadFor customers, there is nothing worse than landing on a website with a product they really want to buy, only to see those three brutal words: out of stock. ❌
Stockouts are still an Achilles heel for businesses, and an expensive one at that. According to research from analyst firm IHL Group, stockouts cost US and Canadian retailers an eye-watering $350 billion in 2022, while labor challenges and supply chain disruptions still wreak havoc on the average customer experience.
While businesses can’t completely avoid these issues, they can mitigate them with smarter inventory management. Thanks to strategies like safety stock and reorder points, businesses can maintain inventory levels to fulfill customer orders while minimizing storage and supplier costs.
So, what is the difference between safety stock and reorder points, and how can they help you sell better? 🤔
This article will teach you just that. Let’s dive in 👇
The nuts and bolts of safety stock
Safety stock is extra inventory kept on hand so products are always available to fulfill customer orders.
Basically, it’s a buffer to minimize stockouts, keep customers happy and build trust in your brand. If you have a physical store, it’s a little easier to keep an eye out to see what products run low. But for online retailers, inventory management needs a more proactive approach.
A surprising number of vendors get safety stock levels wrong and hit shortages. Although unprecedented, research found when COVID-19 struck in 2020, stockouts just in the United States increased to more than 35%, which had a significant knock-on effect on revenues. But the reality is that stockouts can happen for a lot of reasons that an optimized safety stock level solves, like:
Demand
Customer demand fluctuates depending on a multitude of factors like seasonality, market trends and the current economic environment. If you have SKUs with high demand variability, an accurate safety stock level can help you ride the fluctuation wave.
Lead time
Are your product lead times rocky? The longer your lead time, the more safety stock you may have to keep on hand to account for delays.
Service-level agreements (SLAs)
SLAs around customer expectations can influence safety stock levels. If you promise fast fulfillment and speedy shipping times, it usually requires higher levels of stock (and safety stock) to reduce the chances of stockouts.
Supply chains
The more flexible the supply chain, the more likely you are to not have to store a large quantity of safety stock if a supplier cannot fulfill an order or keep up with demand fluctuations.
Finally, the last link in a safety stock chain is supplier reliability. Unreliable suppliers or those prone to delays may necessitate a larger safety stock to compensate for potential disruptions in the supply chain.
The basics of a reorder point
A reorder point is a specific inventory level when an order should be placed to replenish stock so that a company can fulfill customer orders and prevent stockouts.
It’s usually triggered when stock hits a specific point based on customer demand, safety stock levels and supplier lead times.
Identifying the appropriate inventory level for stock reorders can help avoid customer disappointment if one of your products is out of stock. That’s really the main reason for establishing a reorder point — it safeguards your company against not just lost revenue, but reputation damage from customers who might lose faith that you can deliver on a product promise.
Calculating an accurate reorder point can also bring other benefits like:
Efficient inventory levels
Reorder points help keep stock levels just right. You can avoid overstocking (and understocking) which saves costs around storage and excess inventory buys.
More accurate forecasting
Accurate reorder points help you really understand buyer patterns, lead times and supply chain reliability. This data is really important for improving forecasting accuracy and keeping inventory lean while managing sufficient stock levels.
The best thing about accurate reorder points and safety stock levels is that retailers can tie all this data together to improve the customer experience.
Harvard Business Review (HBR) conducted a deep dive on stock levels and low-level inventory after an Instacart experiment involving over 850,000 customers. The experiment looked at what warning customers about possible stockouts had on their buying decision, which found that sharing low item availability helps set realistic customer expectations.
We propose that sharing potentially unflattering low item availability information with customers increases customer trust of the retailer, and consequently their engagement with the platform in the longer term. Our analysis suggests that frankly disclosing which items are most likely to be out of stock can be a winning strategy for online retailers and marketplace facilitators that are suffering from stockouts, potentially improving both customer satisfaction and lifetime value.
Benjamin Knight and Dmitry Mitrofanov
Harvard Business Review
Sounds good, right? Well here’s how to calculate an accurate reorder point for a product 👇
How to calculate your reorder point
Before we jump into reorder point calculations, you must remember this number won’t stay the same.
Reorder points are elastic. They will change depending on factors like seasonality, customer sales cycles, delivery lead times and supply chain issues. With that said, you can get a basic reorder point using this calculation:
(Safety stock + regular inventory + lead order time) * monthly sales = reorder point
Here’s an example.
An online outdoors retailer based in California stocks a really popular pair of hiking boots. On average, the store sells 1,000 pairs a month, has around 10 days in normal inventory levels (330 pairs) and holds five days worth of safety stock (roughly 195 pairs). It also takes the vendor 20 days to receive a new order from their supplier. But there are other issues to take into account:
- Sales are seasonal and demand fluctuates a lot. Hikers go nuts for the boots in summer and early fall, but orders tend to tail off during the winter months
- Lead times aren’t always met. The boots are imported from Germany, so any issues in production or shipping times can delay the order’s arrival by several days
- The boots are expensive, so the online retailer cannot afford to keep a lot of safety stock on hand, especially as a new range of boots is released every year. It opts to keep 300 pairs in safety stock
With these factors in mind, it makes sense for the retailer to give themselves a day (or two) buffer on the product lead time to account for shipping delays. So, let’s calculate the reorder point:
(195 + 330 + 22 days) / 1000 = Reorder point is 1213 pairs of hiking boots
At this point, you may be asking…wait, what’s the difference between safety stock and a reorder point? Surely you just put another order in once you start using up safety stock? 🤔
Wrong. Let’s take a better look at the differences between the two 👇
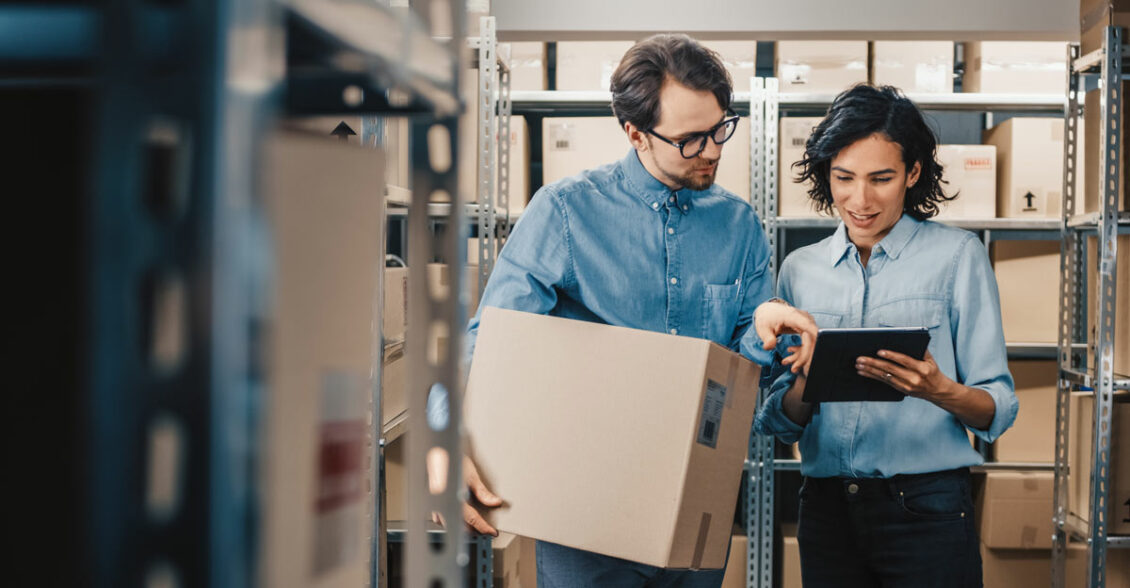
The main differences between safety stock and reorder points
While safety stock and reorder points are related, they both play very different roles in the inventory management process.
Reorder points and safety stock serve different purposes
Safety stock is a buffer for your product inventory. It should be used to avoid unexpected customer demands or issues with your supply chains. Think of it as that emergency pizza that’s shoved at the back of your freezer… you know it’s there, but it should only be busted out if you need it.
On the other hand, the reorder point is the trigger for when inventory needs to be stocked up. This point allows you to avoid touching safety stock while optimizing inventory levels to meet customer demand and minimize overstocking.
Both help demand variations
Safety stock is directly tied to demand variability as it allows businesses to absorb unexpected peaks and troughs in sales. If your business is hit by seasonality boosts, surging sales or just an unexpectedly good period of trading, safety stock helps you capitalize without leaving the customer empty-handed.
Reorder points play a different role with demand fluctuations. Although reorder points are not static, their only job is to keep a continuous supply of inventory in your system. It does help avoid stockouts, but safety stock is the real saving grace in these situations.
Each optimize inventory management (in different ways)
Safety stock helps businesses avoid stockouts and keep customers happy. But safety stock can also be a drag on a business’s finances, as you must pay for extra storage and supplier costs. These costs add up, especially if sales fluctuate or the business is just getting off the ground and funds are low.
An accurate reorder point reduces the amount of excess stock you pay for while still fulfilling customer orders. It helps you strike a happy balance between over and understocking while ensuring your inventory can keep up with customer demand.
The differences between safety stock and reorder points may not be huge, but you must use each to their strengths — and recognize their weaknesses. As long as you use both strategies correctly, you can optimize inventory levels and build trust with customers through fulfilled orders 💰
Keep in mind that, even if you have calculated a basic reorder point for products in your inventory, there are some tweaks you can make in the process:
Monitor your ‘bread and butter’ SKUs
You may have 10 SKUs in your inventory, or 10,000. But there will still be some SKUs that bring in more revenue than others. Prioritize these SKUs and revisit reorder points regularly so you can tweak order timelines or spot issues with supply chains before they impact revenue.
Keep reorder points flexible
Reorder points will change depending on suppliers, customer demand and issues outside of your control. If a supplier increases pricing, extends lead times or stops trading altogether, a flexible reorder point will help you adjust for any changes.
Embrace artificial intelligence (AI)
Last but not least, the smartest move for businesses using reorder points is to invest in AI-powered inventory management software.
It’s impossible to check every product safety stock level and reorder point, especially if you handle tens (or hundreds) of different SKUs. Investing in dedicated inventory management software can automatically track individual products and eliminate any human errors around stock reorder points that are almost impossible to avoid.
For example, Peak’s SKU-level reorder software uses demand forecasting, AI-driven reorder points and safety stock inventory levels to minimize stockouts. It looks at supply predictions and storage capacity to calculate the optimal reorder point for every SKU in your inventory. The result? Lower inventory costs, happy customers and more sales 💰
See Peak's Reorder application in action
Want to learn more about how Peak's AI-driven reorder points can optimize your inventory levels?
Learn more about our application and book a demo here.
More from Peak
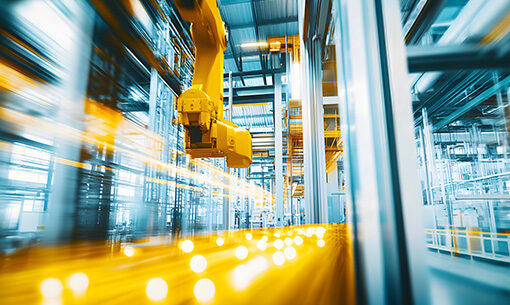
The cognitive layer: how AI-optimized supply chain decisions enable true manufacturing autonomy
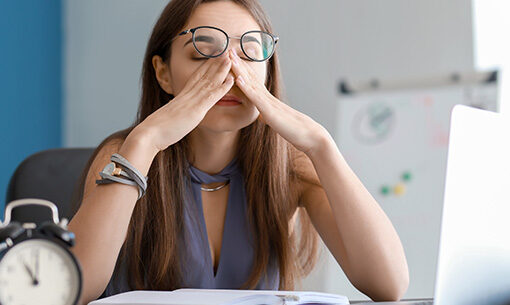